Automated Bagging Machines
Table Top
Production Baggers
Printers
Options & Accessories
Table Top Bagging Machines
T-375 - The table top with all the optionsThe T-300 has the all the great functionality of the T-375 but without the printing option. The T-300 is the ideal simple and cost effective bagging machine.
- Four colour screen with pop-up windows
- Diagnostic and troubleshooting screens
- Preset and totalising bag counter
- Automatic “paced” operation with fill time delay timer
- Universal, adjustable parts chute
- Adjustable support shelf
- Blower with flow controls
- One year limited parts warranty
Cycle operation Automatic paced
Bag size range (10″ rolls) 50mm x 50mm – 2″ x 2″ up to 280mm x 410mm – 11″ x 16″
Guard-switch feature Standard
Product pass-through 75mm upto 130mm 3″ to 5″
Electric 240V/60Hz
Air .50psi
Dimensions 510mm W x 360mm D x 540mm H – 20″ W x 14″ D x 21″ H
Weight 50kgs/ 56kgs – 110 lbs./125 lbs.
The T-375 integrates with APP’s and third party automation machines and devices
Robotics…..The T-375 can also be supplied with an auxiliary interface which communicates with the robotic arm ensuring the bag only cycles when the part(s) are safely in the bag. The interface also tells the robotics if there is a problem, for instance when the T-375 runs out of bags, no parts ending up the floor.
Production Bagging Machines
T-1000 The most reliable bagging machine in the market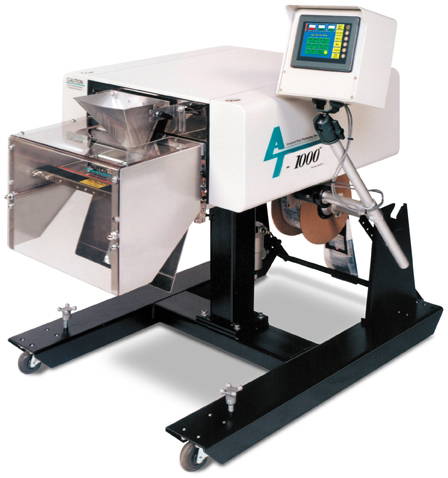
If you need more information…
Dimensions 940mm W x 107mm D / 120mm W 920mm D – 37″ width x 42″ depth 47″ width x 36″ depth
Memory 32 job saves / 999 label saves
Load Height 760mm – 104mm / 30 – 41″
Cycle Rate up to 80 bags/min.*
Seal Bar 138mm / 460mm – 15″ wide bronze 18″ wide bronze
Bag Size Minimum 50mm x 76mm / 100mm x 150mm – 2″ x 3″ 4″ x 6″
Bag Size Maximum 360mm x 760mm / 460mm x 910mm – 14″ x 30″ 18″ x 36″
Product Pass Through Upto 200mm – 4″ (up to 8″)
Electric 240/220V, 60/50Hz 240/220V, 60/50Hz
FLC 10 amps 10 amps
Air 1.5 cfm, 80 psi 1.5 cfm, 80 psi
Touch Screen Funnel,
Foot Switch Guards,
Manual 1 Year Parts Warranty Included – extendable to 24 months
The T-1000 Advanced Poly-Bagger™ can reduce your packaging costs with high speeds, versatility, reliability and simplicity.
- “User-Friendly” Touch Screen Interface Panel: Change settings “on the fly”, turn on counters or other options, control machine speed, or other auxiliary equipment. Programmable for up to thirty settings. Quickly position the operator panel wherever you desire with a long arm extension and ball joint mounting bracket.
- Patented “Teflon Shield™” moves Teflon away from heater bar, except when sealing, for extended Teflon life up to 10 times the life of standard sealers.
- Uses Advanced Poly-Bags™ (pre-opened bags on rolls, manufactured by Advanced Poly-Packaging, Inc.) with sizes ranging from 2″ x 3″ to 14″ x 30″ and thickness from 1 mil to 5 mil. T-1000 “Wide” uses bags ranging from 4″ x 6″ to 18″ x 36″.
- Designed with a small footprint and equipped rugged casters, the T-1000 Advanced Poly-Bagger™ is designed for easy movement to various production cells throughout your plant.
- The T-1000 Advanced Poly-Bagger™ is crafted from the highest quality components and materials to withstand the most rigorous manufacturing environment. We guarantee long life with minimal maintenance (one year parts warranty).
- Energy Conservation & Component Saver provides for extended component life. The T-1000 Advanced Poly-Bagger™ is programmed to turn off components when not in use including the touch screen, motor, air and heater bar.
- Four internal counters are standard: 1) Preset Counter – the bagger stops when the predetermined count has been reached. 2) Totalling Counter – reset this counter at the beginning of each shift or day to record packaging production over a period of time. 3) Continuous Strip Counter – set the number of bags (not separated at the perforation) to feed in a continuous strip. 4) Maintenance Counter – total machine cycle counter for preventative maintenance/component inspection intervals.
- Anti-Jam Device – Detects obstructions in the seal area, automatically reverses the pressure bar and stops the cycle operation.
- Technical assistance screens provide access to INPUT/OUTPUT IO without removing covers.
- Pop-up troubleshooting screens indicate operation messages as well as fault conditions.
Manually slide your product horizontally into the bag, or automatically push the product into the bag and your bagger does the rest! After the product enters the bag, the bagger seals the bag at the loading station and automatically discharges the product on an opptional horizontal take away conveyor or a bin. The next bag is then indexed into position and blown open, ready to receive the next product.
- Adjustable angle – let gravity do most of the work!
- The LC-10 Light Curtain is a standard feature, making your system safer
- Helps meet quality standards because your are closer to the bag and can visually inspect product as it’s entering the bag
- Patented “Next Bag Out” printing option virtually eliminates mislabeled bags
- BO-30 Bag Opening Device is a standard feature that shapes the bag to fit the product for automatic loading applications; also, available as an option
- Standard Touch Screen Operator Panel allows the operator to track production, adjust settings and receive technical operation information. Up to 32 jobs can be saved for instant job changeover. Pop-up numeric keypads and other window and message screens provide fast setting changes and prompt information to operators.
- A Solid Bronze Heater Bar maintains constant heat with “independent action” sealing. Coupled with our patented Teflon Shield and Anti-Jam obstruction detection, we guarantee perfect seals and low maintenance.
- A horizontal flat belt conveyor removes product from the sealing area to further packing stations. Increased product pass-through for products up to 8″ thick.
- Compact design to “fit” in any packaging operation (shown below with optional Ti-1000 Thermal Transfer Printer). Print inline while loading your product; stop applying pressure sensitive labels. Print part numbers, text, logos, graphics and bar codes directly to the surface of the bag. See the Ti-1000 Thermal Transfer Printer Product page for details.
- Stainless “Slide” Plate provides a low friction surface with easy-open bag and product guides.
Dimensions 36″ width x 81″ long
(including 3′ conveyor) 47″ width X 93″ long
(including 4′ conveyor)
Memory 32 job saves 32 job saves
Load Height 40″ 40″
Cycle Rate 100 bags/min.* 100 bags/min.*
Seal Bar 15″ wide bronze 18″ wide bronze
Bag Size Minimum 3″ x 5″ 4″ x 7″
Bag Size Maximum 14″ x 30″ 18″ x 30″
Product Pass Through Up to 200mm – Up to 8″
Electric 240/220V, 60/50Hz 240/220V, 60/50Hz
FLC 10 amps 10 amps
Air 1.5 cfm, 80 psi 1.5 cfm, 80 psi
Touch Screen Funnel, Foot Switch, Guards
Manual 1 Year Parts Warranty Included Included
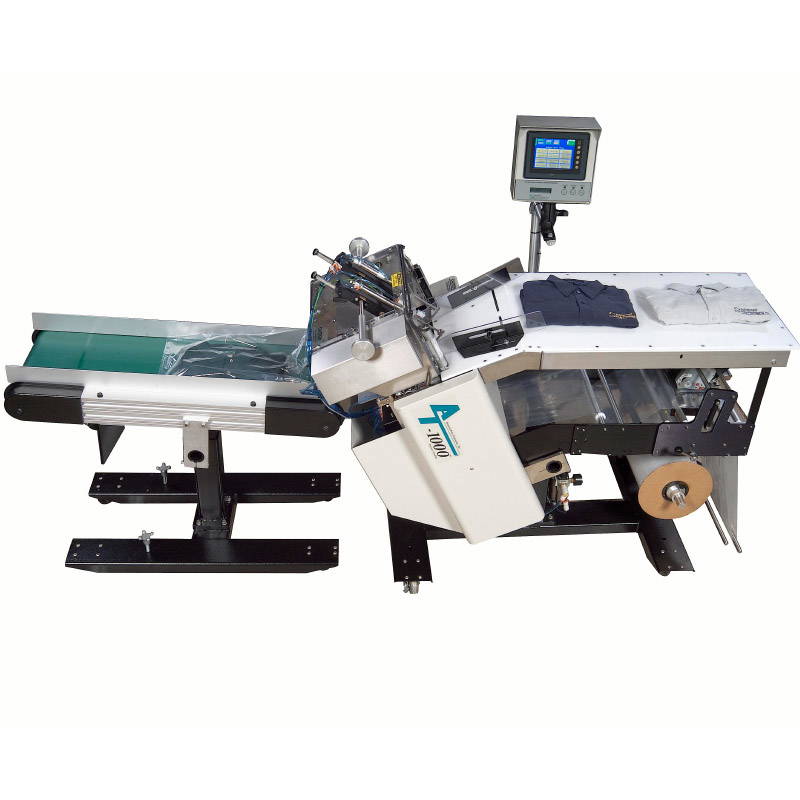
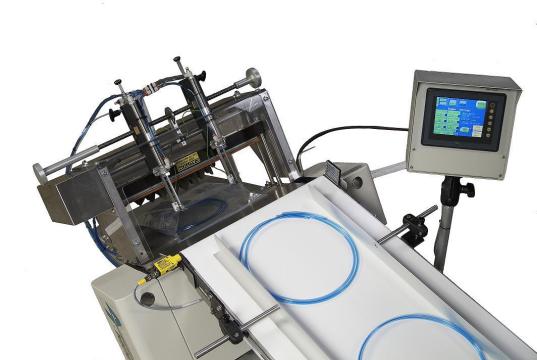
Length 3′ Standard (up to 100′) 4′ Standard (up to 100′)
Height Adjustable Height & Tilt Adjustable Height & Tilt
Belt Speed Up to 50’/min. Up to 50’/min.
Motor 1/8 HP, DC 1/8 HP, DC

Fastest Printer on the Market
Special Features:
• Perforation or photo optic registration system for precise thermal print registration
• Perfectly integrated with the T-1000, the Ti-1000Z RAP is operated from a single touch
screen that also controls the bagger.
• 203, 300 or 600 dpi print resolution available
• 4”, 5” or 8” wide print heads available
• Film accumulator for continuous feeding and tension control
• Full color touch screen/PLC operation with alarm outputs